Innovation In Practice – First Onshore UK Application Of Latest Flow Stop Technology
By Phillip Shortt, Gas Transmission Operations Engineer at Mutual Energy and winner of the YPPC 2024
Introduction
The Belfast Transmission Pipeline (BTP) has a 600mm nominal diameter and 75bar, is the main entry point for natural gas entering the Northern Irish natural gas system from Great Britain. It currently flows all of the gas that is provided to the power stations and Distribution Network Operators (DNOs) in Northern Ireland.
Constructed by British Gas in 1996, the BTP was originally intended to continue from its current terminus in Belfast towards the Republic of Ireland (ROI), linking the NI and ROI systems.
This would allow gas to flow through two entry points into the Belfast network with an N+1 level of resilience. On this understanding, engineers ‘risk-assessed-out’ the need for a block valve on the 26km length from Ballylumford to Carrickfergus.
Over time however, the transmission network evolved differently. With an offtake being constructed in 2004, this created the back up for the BTP, from ROI, at the midpoint rather than the end of the BTP. This introduced a security of supply risk to the BTP.
Due to the lack of a block valve upstream of the new connection, a damage anywhere along the entire 26km length of the BTP would require complete isolation of two (of three) of Greater Belfast’s city gate supply sites and, potentially, the loss of gas supply to a significant number of customers.
In 2020, Mutual Energy (MEL) received a request to provide a transmission connection from the BTP on a tight schedule to facilitate the environmental benefits of replacing two substantial coal fired power generation units with natural gas.
This presented an opportunity to cut a full-bore block valve (BV) into the main line in conjunction with the transmission spur. A block valve at this particular location would significantly reduce the security of supply exposure of Greater Belfast’s customers.
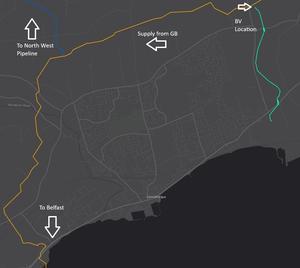
FIGURE 1 - NETWORK LAYOUT AND BV LOCATION
The question then became, how best do we perform a full bore cut out on Northern Ireland’s arterial gas pipeline, safely, economically and maintaining full flow of gas?
The solution
Given the criticality of the BTP to the whole NI gas system, MEL were acutely aware that there was no way that the pipeline could be fully isolated to allow the cutting in of the new block valve.
It was obvious from the outset that a bypass and flow stopping would be required. Several solutions were considered, including traditional flow stopping techniques that have been in place for over fifty years.
This technique is used widely within the onshore UK gas transmission industry, is well understood and has a successful and reliable track record.
In developing emergency repair strategies for our submarine pipelines. we had become aware of the innovative STATS BISEP tool. The flow stopping unit has two hydraulically actuated seals and an integral bleed point between the seals which provides the ‘double block and bleed’ within the one unit.
With traditional means of flow stopping at these high pressures, two units with single seals and a separate bleed point in the middle would be required, at minimum.
The tool would work similarly to the diagram presented.

FIGURE 2 – ANTICIPATED FLOW STOPPING ARRANGEMENT
Back in 2020 when considering the suitability of this technology, while it had been applied successfully to hundreds of pipelines of multiple diameters and some of much higher pressure than our 75bar, it had not been adopted by or attempted within the UK onshore gas transmission sector.
The potential advantages were such that we believed it right to assess the risks in being industry pioneers.
These were:
- · Fewer pipeline interactions – Reducing the risk to the live pipeline while welding on the required fittings to facilitate implementation with fewer expensive fittings to procure
- · Built in bypass through the tool – Maintaining the flow through the BTP, and by extension the NI gas transmission network.
- · Complete double block and bleed 100% isolation – Increased safety for operatives on the ground.
- · DNV Approval – Independent verification by leading experts
- · Smaller site footprint – Reduced civils cost
- · Potentially fewer vented emissions
Having gone through internal evaluations and assessments, assisted by engineering consultancy PIE, the tool was recommended through our corporate governance processes and ultimately approved for adoption by our board Risk Committee.
Several challenges were still present before physical deployment on the live system.
These were:
- · Developing a program for deployment, including design, commercial procurement, FAT, NROs and pre-deployment Field Trial
- · Designing the offtake accounting for BISEP tool deployment and bypass requirement
- · Following detailed design, procuring the tool and hot tap connection vendor
- · Developing pre-deployment FAT
- · Conduct HAZID/HAZOPs and developing appropriate procedures to control the connection operation in agreement with MERC, the connection vendor and tool supplier
Implementation
Successful approval and award of contracts was followed promptly by enabling the works in advance of the tools deployment. This included a large civil excavation to expose the pipeline, providing room for the tools, new block valve and offtake arrangement for the new connection.
Welding of fittings under pressure to the pipeline included high levels of NDT pre-inspection to ensure the integrity of the parent material. This, for example, included MPI, radiography and checks for laminations amongst others.
Flow conditions within the live pipeline had a potential to cause issue during the welding procedure by removing heat too quickly from the welds, introducing risk of defects.
Contingencies involved power stations downstream potentially nominating their gas capacity at alternative entry points, with a further contingency of adjacent network operators being prepared to reduce flows in their networks, had to be agreed.
If it had been set up in advance of the welding, these could have been activated to reduce the flow in the pipeline to prevent the rate of temperature decay if necessary.
During the days, fortunately, a large power generation unit was out, keeping the welds in the goldilocks zone; a positive to avoid enacting the contingencies, and additional costs thereof.
Slab valves were installed to the welded tees to facilitate access to the live pipeline system following hot tap.
Under pressure drills were then used to commission the access points for the BISEP tool as shown in the sequence below:
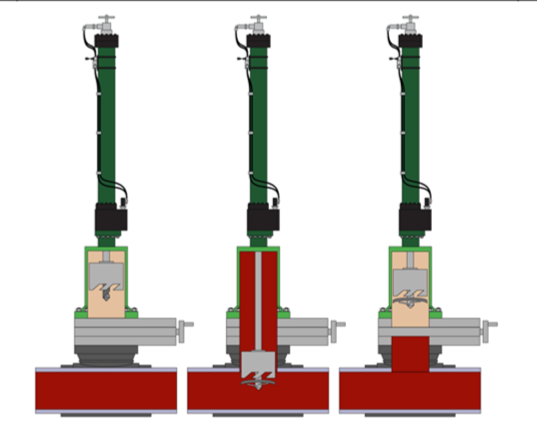
FIGURE 3 – HOT TAP SEQUENCING
The BISEP tools were then installed onto these access points ready for deployment, however, to maintain continuity of supply, the bypass needed to be in place and commissioned prior to tool deployment.
The bypass required to facilitate this operation was calculated to be DN400, taking account of the maximum velocities for unfiltered gas in IGEM/TD/1.
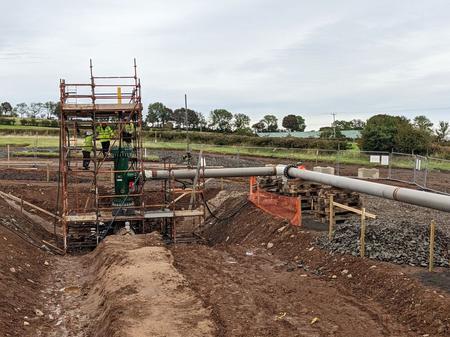
FIGURE 4 – INSTALLED TOOL AND COMMISSIONED BYPASS
To quote Rabbie Burns, “The best-laid plans of mice and men oft' go awry”. When it came to the actual flow stopping operation, we hit an unforeseen snag.
Upon deployment of the seals into the pipeline, there were very marginal levels of let-by on the upstream side of the isolation, which STATS were unhappy with. Taking a step back, all parties got together to assess whereby the problem was identified. This was swarf from the hot tap lying in the pipeline preventing a flush seal.
Previously, the tool has been used offshore on high flow pipelines and as such swarf was quickly blown downstream out of the way of the sealing face. With the modest flows in this pipeline at the time, this did not happen.
The remaining swarf can be seen in the figure below:
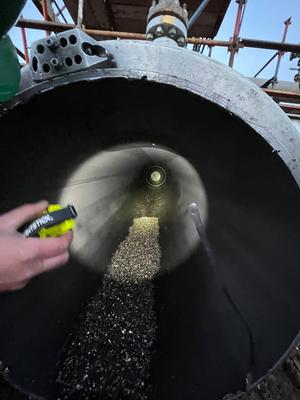
FIGURE 5 – SWARF INSIDE THE PIPELINE
At this point it was all hands to the pump, and within hours STATS had come up with a solution involving ‘sweeping’ the swarf using the sealing head, gathering the swarf in grease before removing.
This proved to be very successful. Following the replacement of the seals flow, stopping was achieved in late October 2022.
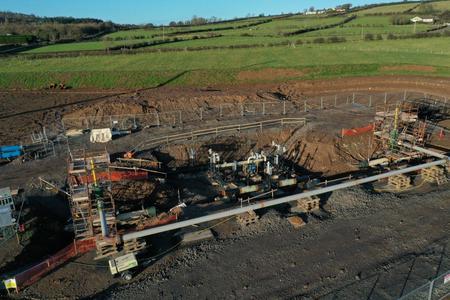
FIGURE 6 – SITE DURING ISOLATION SHOWING NEW BV ARRANGEMENT
The isolation allowed decommissioning, cutting and welding in of new arrangement to the BTP to occur, without a single mbar of let by during the process.
The new arrangement was gassed up and the tools and bypass successfully removed.
As an operator, all we are left with now are two full bore top tee flanges with completion plugs to manage enduringly, which is greatly preferred to many smaller buried fittings.
Gas is now flowing to the power generator, and all this was achieved without interruption to the end user.
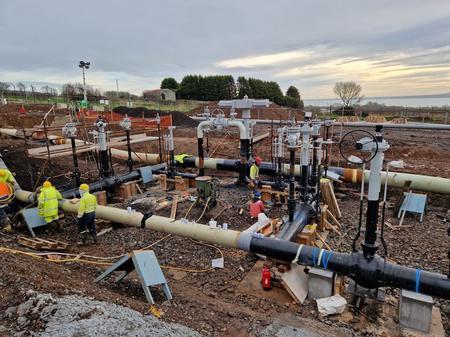
FIGURE 7 – COMPLETE TIE IN FOLLOWING TOOL REMOVAL
Keeping in touch with STATS, we know steps have been taken to mitigate the issue of swarf, including procurement of spare seals and sweeping with the BISEP head in low flow pipelines.
Other innovations are being developed including a swarf management system, currently in testing. Mutual Energy are proud to have teamed up with STATS Group on this innovative project.
From the offset, using pioneering technology might have been considered higher risk, but the fact there were so fewer interventions needed to such a critical pipeline, it reduced risk and lowered costs.