IGEM/UP/2 Edition 3 - Installation pipework on industrial and commercial premises
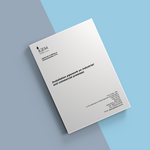
This standard applies to installation pipework and pipework downstream of any plant isolation valve that is not "appliance pipework", on industrial and commercial premises. It deals with the design, installation, operation and maintenance of pipework designed to carry 2nd or 3rd family gas in the gaseous state with MOP not exceeding 60 bar. It considers pipework of steel, stainless steel including corrugated stainless steel tubing, copper and polyethylene.
Specifically it contains details of:
- Legislation and standards such as Gas Safety (Installation & Use) Regulations
- Planning and design, along with material selection
- Jointing processes for multiple material types
- General principles for installing pipework
- Principles for installing buried pipework
- Entry into and exit from buildings
- Pipework in ducts, etc. in buildings
- Pipework in multi storey and multiple dwelling buildings
- Pipework support
- Flexible connections
- Manual valves
- Vents and breathers
- Compressors, boosters and pre-mix machines
- Procedures on completion of installation.
Introduction
1.1 This Standard supersedes IGEM/UP/2 Edition 2, Communication 1729, which is obsolete.
1.2 This Standard has been drafted by an Institution of Gas Engineers and Managers (IGEM) Panel, appointed by IGEM’s Gas Utilization Committee, and has been approved by IGEM’s Technical Co-ordinating Committee on behalf of the Council of IGEM.
1.3 This Standard covers the design, installation, commissioning, operation, maintenance and decommissioning of gas installation pipework with a MOP not exceeding 60 bar on large domestic and on industrial and commercial premises. This includes compressors, boosters and pre-mix machines with an upper limit on discharge pressure of 500 mbar on industrial and commercial premises. Due consideration of the requirements of BS EN 1775 and BS EN 15001 has been made.
1.4 This Standard applies to new installations as well as to replacement of, or extension to, existing installation pipework. It is not retrospective but it is recommended that existing installations be modified to meet this Standard, when appropriate.
1.5 Under normal circumstances, correctly jointed pipework will not leak throughout its lifetime. However, the local environment, mechanical damage and interference could cause leakage to occur. Therefore, it is necessary to ensure that if leakage does occur, a dangerous condition will not result. New advice is given in this Standard on the location of pipework joints.
1.6 Advice is given in this Standard relating to classification of hazardous areas for Natural Gas (NG) installations. Further information is provided in Appendix 9.
Note: For other gases, such as Liquefied Petroleum Gas (LPG), additional advice may be available from the fuel supplier or by referring to Energy Institute guidance EI IPMSCP-P15.
1.7 For new installations, a documented risk assessment of the design and work activities is carried out to minimise the risk of danger to the installer, the client, operators, third parties and property. For existing industrial and commercial installations, the Dangerous Substances and Explosive Atmosphere Regulations (DSEAR) require the completion of a risk assessment, with improvements made as are reasonably practicable without excessive cost. For such installations, it is essential that they are maintained and inspected as determined by the risk assessment.
Gas pipework design and installation for industrial and commercial installation undertaken in accordance with this Standard has to account for any requirements imposed by DSEAR. However, it is acknowledged that a DSEAR risk assessment may be undertaken, by others sometime later, on the completed installation. Such an assessment could identify issues with the gas installation, which may have arisen as a result of subsequent work undertaken by others on the site after completion of the gas installation or of site specific risks subsequently indentified. It is acknowledged that such issues cannot be assessed at the design or installation stage.
1.8 Terms such as “maximum operating pressure” (MOP), “maximum incidental pressure” (MIP), “operating pressure” (OP), “lowest operating pressure” (LOP) and “design minimum pressure” (DmP) were introduced in IGEM/UP/2 Edition 2 to reflect gas pressure terminology used in European standards.
Other terms were introduced to assist in recognition of design information to be transferred between interested parties.
Referring to Figure 1, attention is drawn to how OP oscillates about the set point (SP). Note also that MOP can be declared at a higher value than OP. The strength test pressure (STP) has to exceed MIP. This means that, at least with respect to integrity, the installation will withstand a fault pressure from the upstream system. Safe operating limit (SOL) is a requirement of the Pressure Systems Safety Regulations (where applicable).
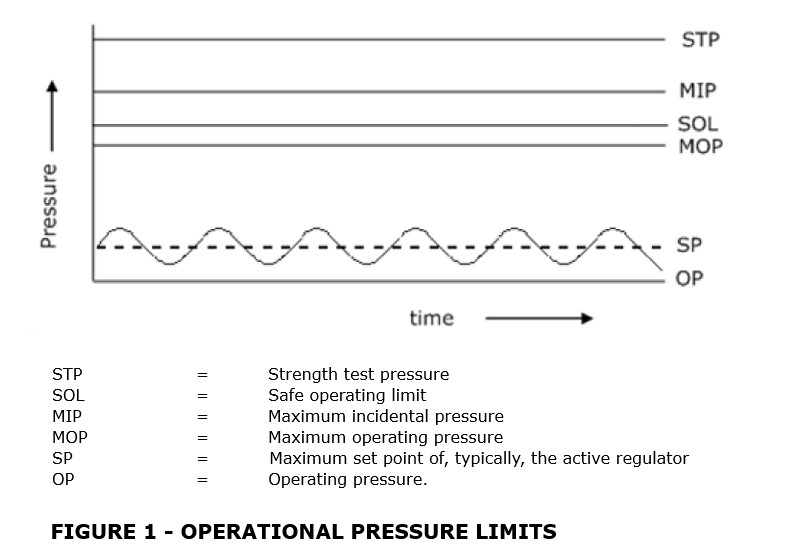
1.9 This Standard makes use of the terms “must”, “shall” and “should” when prescribing particular requirements. Notwithstanding Sub-Section 1.12:
- the term “must” identifies a requirement by law in Great Britain (GB) at the time of publication
- the term “shall” prescribes a requirement which, it is intended, will be complied with in full and without deviation
- the term “should” prescribes a requirement which, it is intended, will be complied with unless, after prior consideration, deviation is considered to be acceptable.
Such terms may have different meanings when used in legislation, or Health and Safety Executive (HSE) Approved Codes of Practice (ACoPs) or guidance, and reference needs to be made to such statutory legislation or official guidance for information on legal obligations.
1.10 The primary responsibility for compliance with legal duties rests with the employer. The fact that certain employees, for example “responsible
engineers”, are allowed to exercise their professional judgement does not allow employers to abrogate their primary responsibilities. Employers must:
- have done everything to ensure, so far as it is reasonably practicable, that “responsible engineers” have the skills, training, experience and personal qualities necessary for the proper exercise of professional judgement
- have systems and procedures in place to ensure that the exercise of professional judgement by “responsible engineers” is subject to appropriate monitoring and review
- not require “responsible engineers” to undertake tasks which would necessitate the exercise of professional judgement that is not within their competence. There should be written procedures defining the extent to which “responsible engineers” can exercise their professional judgement. When “responsible engineers” are asked to undertake tasks which deviate from this, they should refer the matter for higher review.
1.11 It is now widely accepted that the majority of accidents in industry generally are in some measure attributable to human as well as technical factors in the sense that actions by people initiated or contributed to the accidents, or people might have acted in a more appropriate manner to avert them.
It is therefore necessary to give proper consideration to the management of these human factors and the control of risk. To assist in this, it is recommended that due regard be paid to HSG48 and HSG65.
1.12 Notwithstanding Sub-Section 1.9, this Standard does not attempt to make the use of any method or specification obligatory against the judgement of the responsible engineer. Where new and better techniques are developed and proved, they ought to be adopted without waiting for modification to this Standard. Amendments to this Standard will be issued when necessary, and their publication will be announced in the Journal of the Institution and other publications as appropriate.
1.13 Requests for interpretation of this Standard in relation to matters within its scope, but not precisely covered by the current text, need to be addressed in writing to Technical Services, IGEM, IGEM House, High Street, Kegworth, Derbyshire, DE74 2DA and will be submitted to the relevant Committee for consideration and advice, but in the context that the final responsibility is that of the engineer concerned. If any advice is given by or on behalf of IGEM, this does not relieve the responsible engineer of any of his or her obligations.
1.14 This Standard was published in June 2014.
Scope
2.1 This Standard applies to installation pipework, as described in Table 1.
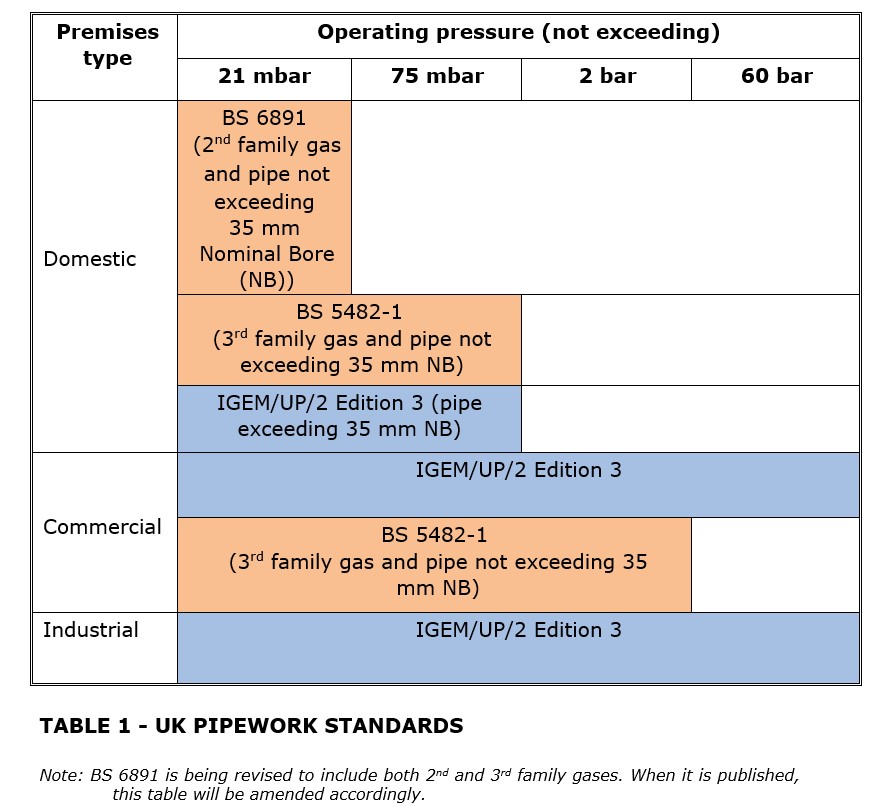
2.2 This Standard applies to installation pipework designed to carry flammable gas, with MOP not exceeding 60 bar, including lighter than air 2nd family gases (for example Natural Gas (NG) and many bio-gases) and heavier than air 3rd family gases in the gaseous state (for example butane and propane gas (LPG) and some bio-gases).
Note 1: It is likely that many of the requirements will be appropriate for lighter than air gases such as 1st family gases, for example Towns Gas, and other bio-fuel gases which have a significant concentration of hydrogen or carbon monoxide, such as those generated from pyrolysis bio-mass processes. In such cases, it is vital that account is taken of their different constituents, condensates and acidic/sulphur content and the consequent effect on materials and operations. It is essential to consider that hydrogen has a far higher flame speed than many other gases and that carbon monoxide is a very poisonous gas.
Note 2: Gases with a specific gravity less than 0.8 can be considered as lighter than air. Other gases may exhibit both heavier and lighter than air properties.
Note 3: Bio-gases will generally not be of consistent quality or pressure and may not have the significant odour associated with Natural Gas.
Note 4: Installation pipework also includes site pipework used for the distribution of flammable gases which are generated on site, such as biogas from anaerobic digestion.
Note 5: Hydrogen and hydrogen enriched gases are not covered by this standard as they require special attention with regard to component materials and jointing techniques.
Note 6: LPG is normally in the gaseous state in systems of MOP not exceeding 2 bar due to its physical characteristics.
2.3 This Standard applies to new installations as well as to replacement of, or extension to, existing installation pipework.
2.4 For NG, this Standard covers installation pipework arrangements as described in IGEM/G/1 (see Figure 2A-2D).
For LPG, this Standard covers installation pipework arrangements described in ACoP L56 (see Figure 2E).
Note 1: Pipework upstream of a primary meter installation and, hence, upstream of installation pipework, is covered by the Pipelines Safety Regulations (PSR) and GS(M)R, IGE/TD/4, IGE/TD/3, UKLPG CoP 22, IGEM/TD/1 and IGEM/G/5 respectively. Under certain circumstances, including where a “Landlord” distributes gas from the outlet of a bulk meter to consumers in a multi-occupational building, the pipework may be designed in accordance with this standard. The ownership and responsibilities may differ and reference is to be made to IGEM/G/1.
Note 2: Meter installations are covered by BS 6400, IGE/GM/4, IGEM/GM/6, IGE/GM/8 and IGEM/G/5 respectively.
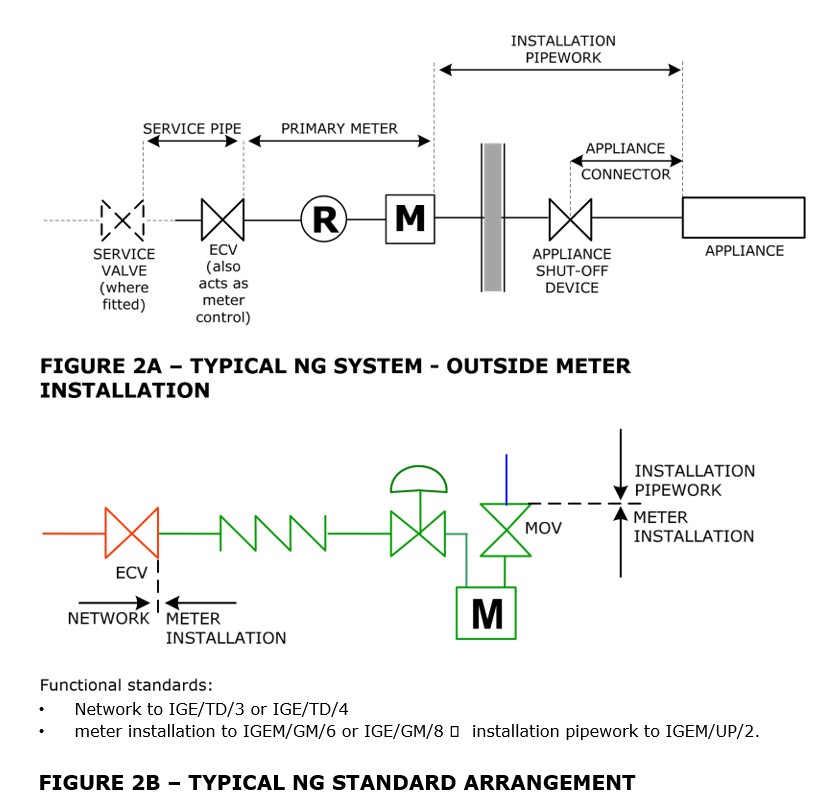
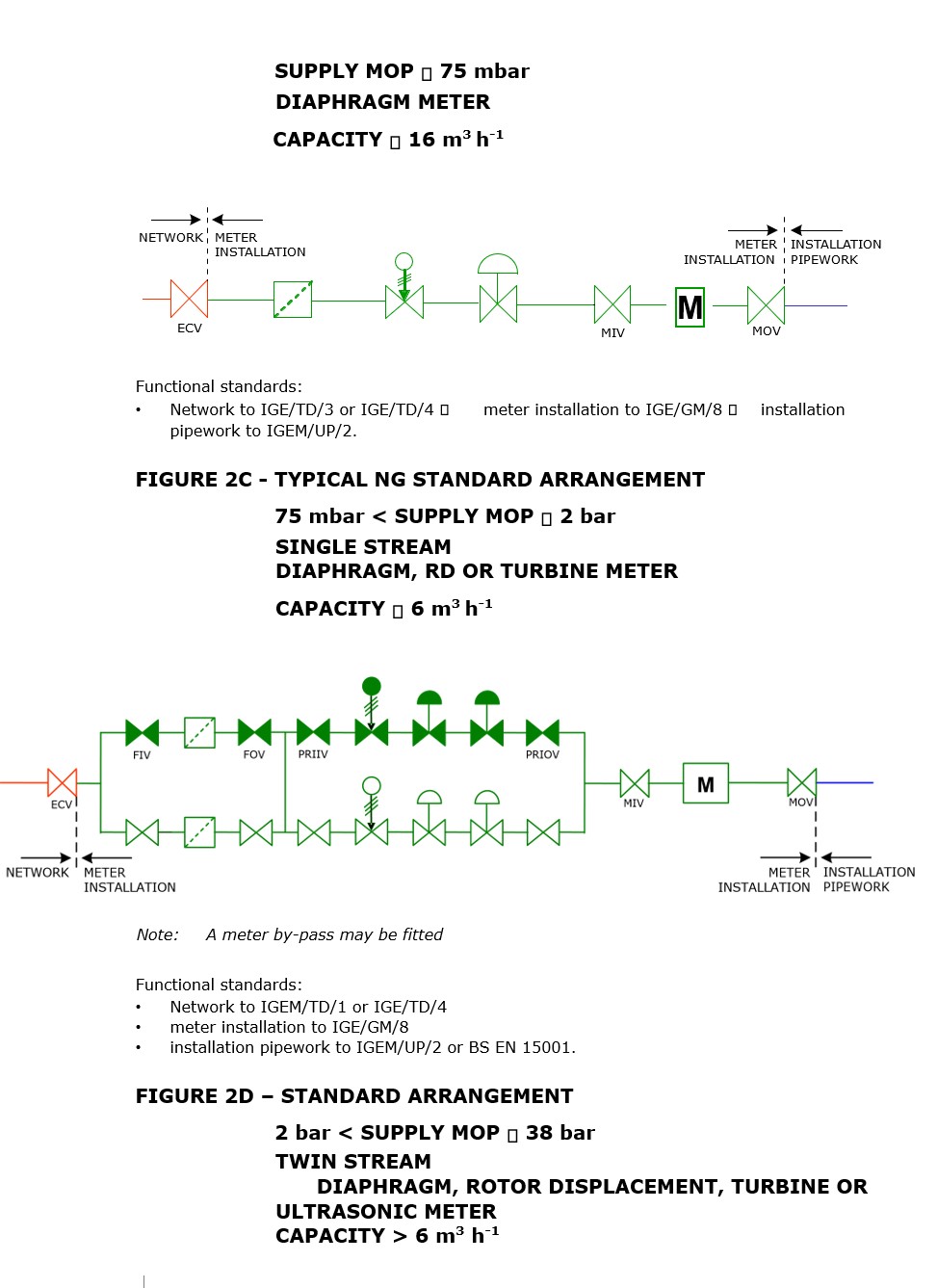
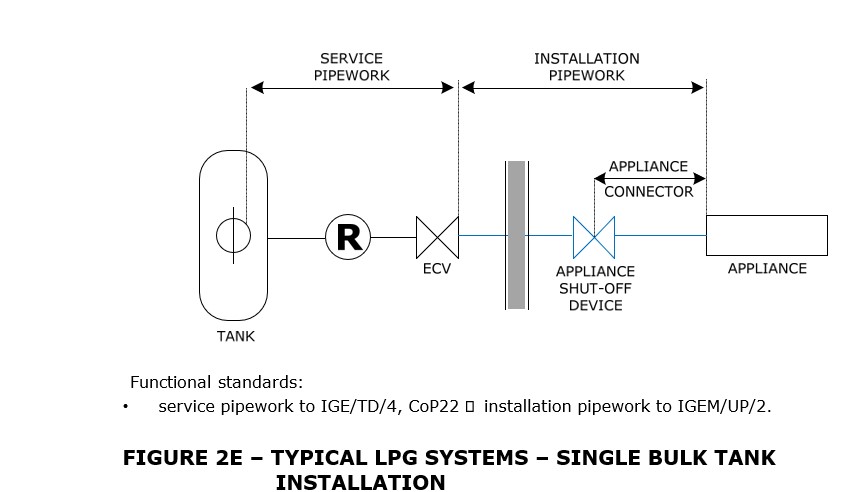
2.5 This Standard deals with the design, installation, commissioning, operation, maintenance and decommissioning of pipework, including selection of materials and components.
2.6 This Standard considers specifically pipework of steel, stainless steel, pliable stainless steel, corrugated tubing, copper and polyethylene (PE). In certain applications, the use of other materials may be specified, and these are required to be used in accordance with their appropriate standards and the principles of this Standard for materials of similar properties.
When considering components of pipework, for example valves, this Standard covers a large selection of the type of materials with which they are constructed. However, the information provided could be subject to change by the manufacturer or by a change in the material specification and reference needs to be made to the latest manufacturer’s data.
2.7 This Standard applies to pressure-raising and pre-mix machines having an upper limit on discharge pressure of 500 mbar.
Note: For higher discharge pressures, requirements are given in IGEM/UP/6. Requirements for pre-mix machines will be provided in the next edition of IGEM/UP/12.
2.8 The term "diameter" refers to nominal inside diameter for carbon, stainless steels and pliable stainless steel corrugated tube and to nominal outside diameter for copper and PE, unless otherwise stated (for example when "nominal bore" is the relevant parameter), see Glossary in Appendix 1.
2.9 Pressures quoted are gauge pressures unless otherwise stated.
2.10 Italicised text is informative and does not represent formal requirements.
2.11 Appendices are informative and do not represent formal requirements unless specifically referenced in the main sections via the prescriptive terms “must”, “shall” or “should”.